Al Rebass is a versatile company specializing in Iraq’s poultry sector and is the country’s largest table egg producer. Al Rebass is, however, a newcomer to the broiler industry, one reason why the company appreciated Marel’s genuine straightforward guidance. Marel’s support allowed Al Rebass to make significant steps in designing the building and preparing an optimal interface between building and equipment.
Marel suggested making the building bigger than originally intended, to make space for internal transport systems and expected future expansions to cut-up, filleting and packing. Al Rebass, an enthusiastic company, was willing to follow Marel’s advice and made more space. All this resulted in positive energy on both sides to get things done.
Al Rebass puts its trust in Marel
Iraqi company starts a greenfield processing plant with further processing and water treatment
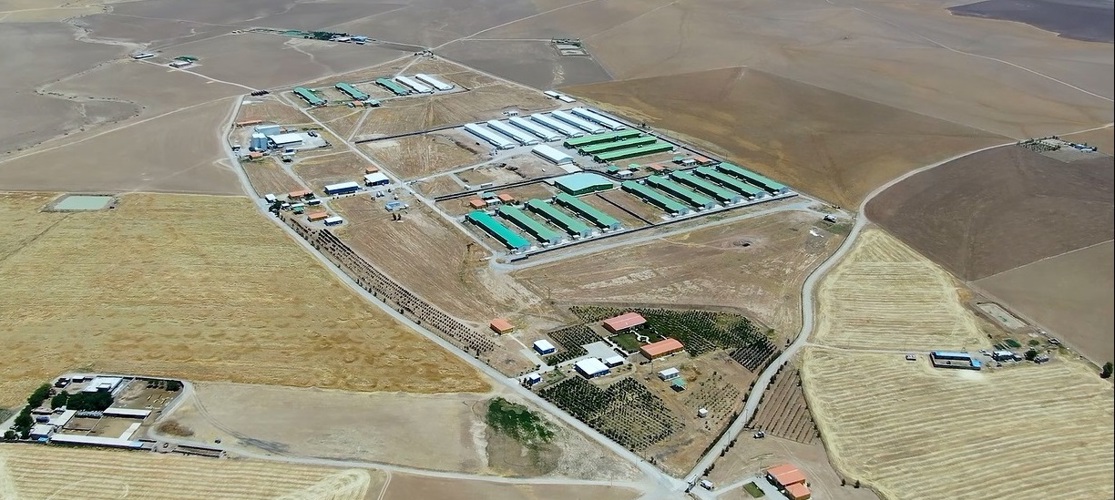
Al Rebass is located near Erbil, which is in Iraqi Kurdistan. The company is setting up a 6,000 bph [100 bpm] greenfield processing plant in a market, which is opening up and gradually moving towards industrial processing. Al Rebass has chosen Marel as its partner for processing equipment and will also install Marel further processing and wastewater treatment systems.

Live bird handling
Al Rebass chose a crate system for live bird supply. Marel is supplying an up/down semi-automatic crate unloading system and an in-line washing system. Live birds are shackled to the line and go straight to the kill station without stunning, as birds have to be processed halal. After scalding and plucking using Marel systems, products are rehung automatically to the evisceration shackle. The VOC combined vent cutter/opening machine starts the evisceration process, which is completed by a Nuova 20 eviscerator.
Inspection and washing
Once products have been eviscerated, they pass through a NIC neck flap inspection machine with an integrated inside/outside washer. While removing crop residues, which contain feed with a high bacteriological content, this machine also gives each product a thorough wash both inside and outside. A separate I/O Washer is no longer necessary. Al Rebass also uses two lung suction guns as an alternative to a FIM Final Inspection Machine.

Fully automated giblet processing
Al Rebass chose to fully automate their giblet process, as there is a good retail market in Iraq for this product. The viscera pack line, to which packs are rehung after having been removed in the Nuova 20 eviscerator, passes a Nuova PGI which removes intestines and gallbladder. The PGI contributes to much improved biosecurity and quality, as intestines and their feces are removed immediately and can no longer cross-contaminate. Removing gall bladders automatically is much better than doing this job manually. Livers stained with gall are now a thing of the past. Livers are automatically harvested using a PLH carrousel machine and a liver inspection conveyor. Gizzards are cut in the PEC and harvested in the MG-150. A washing conveyor and gizzard peeling table follow. Finally, an HLS separates lungs and hearts. All giblets end up in crates, are stacked on a dolly and moved to cold storage.

Whole chicken and cut-up
Chilling takes place in two CounterFlow screw chillers, followed by a dripping drum. Products are then manually rehung to the distribution line. They pass an in-line weighing station and lighter products are unloaded automatically into bins. Innova PDS software ensures the best possible product distribution, contributing to optimum yield. Whole products are packed in plastic bags for distribution as griller. The packing line also includes a special area for selected premium products packed in exclusive boxes. In Iraq, the chicken market is about 70% whole chicken and 30% cut-up with the latter growing quickly. Heavier broilers proceed to an ACM-NT Compact cut-up line, where they are cut into standard breast, wing, and leg portions.
Family Packs
Being the first in Iraq to introduce Family Packs, a fixed weight collation of different portions on a tray, Al Rebass has high expectations for this typical Middle Eastern product. They are aiming for a similar situation to Saudi Arabia, where Family Packs currently make up 30% of the market. As Al Rebass already needs TargetBatcher to make fixed-weight packs, it was only logical to invest in a pre-fill line for making Family Packs. In the pre-fill line, operators put drumsticks, breasts and thighs in the tray. Once this is done, TargetBatcher automatically adds wings until the target weight of 900 g has been reached. Cut wings, legs, thighs and drumsticks not needed for Family Packs will be packed fixed weight for sale retail. Breasts proceed to the AMF-i deboning system. Fillets are then also packed on fixed-weight trays. At the end of the process, an MCheck2 checkweigher and a WeighPrice Labeler label the trays, after which they are packed in boxes for sending to the distribution center.
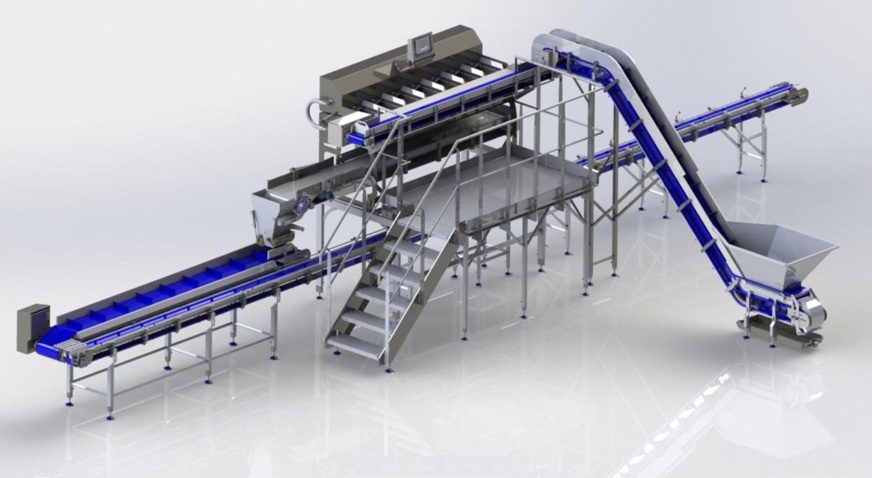
Further processing
Al Rebass also asked Marel to equip the further processing department. Their end products, nuggets, strips and burgers, formed the starting point for Marel to design a made-to-measure convenience food production system. First, the meat preparation system grinds and mixes residual carcass meat to process it into a useable meat mass. RevoPortioner then forms it into the desired product shape to be followed by a 600 mm Coating Line. In collaboration, Active Flour Applicator, Active Tempura Applicator, Active Mixer and RevoBreader make coatings for nuggets and schnitzels. A GoldFryer and LinearOven round off the production system, while a 14-head Multihead Weigher IQF takes care of packing after freezing. Besides convenience food, Al Rebass also wants to produce chicken sausages such as frankfurters, hotdogs and cocktails. The meat preparation line therefore includes an emulsifier. Sausages can then be produced using linking, smoking, peeling and packaging equipment.
Wastewater treatment
Al Rebass discharges its water in nature. It must therefore be treated according to local legislation. Al Rebass and Marel have put together a complete wastewater treatment system. It includes pre-treatment, a Static Screen (a fine screen sieve which collects and discharges all coarse parts larger than 1mm) and a Dissolved Air Flotation unit (pushing all fat to the surface, where it is scraped off and discharged). Bacteria then have to get involved in the process. In the first basin, sludge is separated from clean water using surface aeration according to the BioArt principle. Once water has been purified, the next clarifier basin takes care of sludge sedimentation. This configuration using two separate tanks allows Al Rebass to feed the tank continuously with dirty water and discharge purified water at the same time.
Company website: rebasspoultry.com
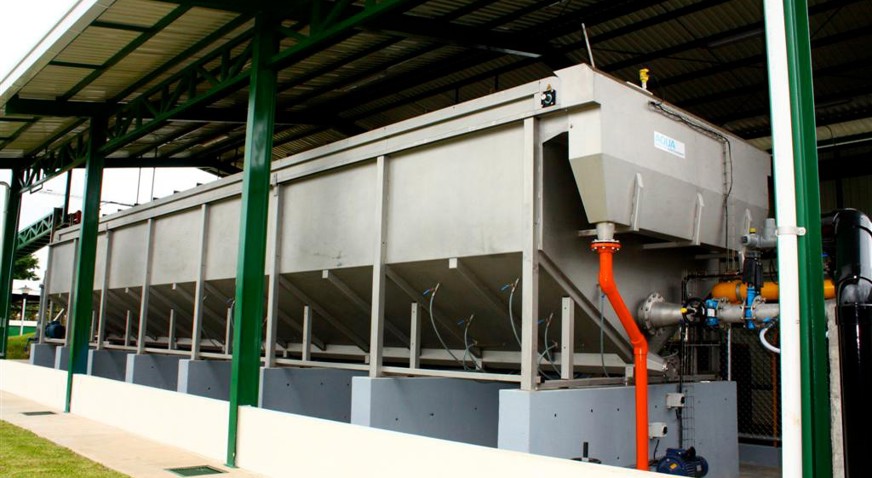
Get in touch
Our dedicated team is here to help and answer any questions you may have. Please complete the form, and we’ll get back to you as soon as possible. We look forward to hearing from you.